Precision Manufacturing Solutions by ATD
Precision manufacturing is essential for industries that demand tight tolerances, consistent durability and reliable performance. ATD delivers precision metal stamping solutions that meet strict specifications across automotive, transportation and industrial sectors. Every part we produce reflects our commitment to quality, speed and measurable results.
If you’re asking, what is precision manufacturing, it’s a disciplined process that combines technical expertise, advanced technology and proven methods to create parts that perform reliably in critical applications. At ATD, precision manufacturing means accuracy, consistency and a production system built around manufacturing efficiency and quality control in manufacturing at every stage.
Today’s manufacturers face growing pressure to shorten lead times, reduce costs and improve product quality all at once. ATD’s solutions address these challenges directly, providing both production scalability and zero-tolerance quality — key factors for competitive advantage.
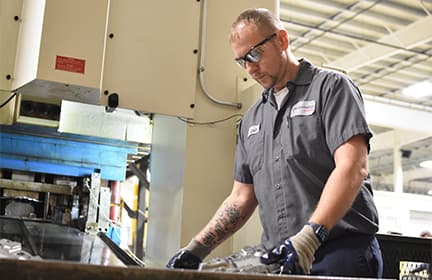
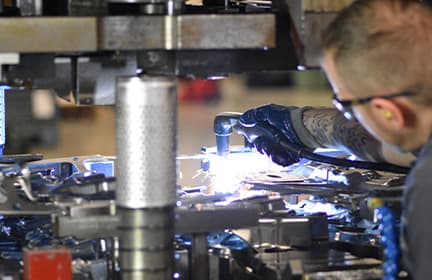
Expertise in Precision Manufacturing Across Industries
ATD’s manufacturing facility is equipped with high-tonnage servo and mechanical presses, advanced metrology equipment and efficient tooling transfer processes. Our approach is built around scalable, repeatable processes designed for high-volume industries where part consistency, delivery speed and manufacturing efficiency are non-negotiable.
We focus on three pillars of manufacturing excellence:
-
Quality Control in Manufacturing — delivering consistent, reliable parts with minimal variability
-
Prototyping Solutions — supporting innovation and speed to market with effective prototype metal stamping processes
-
Production Efficiency — maintaining speed and precision without sacrificing part performance
Customers struggling with vendor delays, part inconsistencies or rising costs can rely on ATD’s stable processes, which have been fine-tuned through decades of experience. We understand that downtime or scrap costs eat into profitability, so every program is designed for efficiency, transparency and speed. Our Can-Do approach ensures customers receive high-performance parts and dependable service throughout every project.
.jpeg)
5 Recent Innovations in Tool and Die Manufacturing
Innovation drives better quality, faster lead times and more reliable production. See what’s shaping the future of metal stamping.
Industry Sectors Served
Automotive
ATD provides precision metal stamping solutions for automotive manufacturers, producing safety-critical parts like seatbelt housings, airbag mounts and lightweight structures for electric vehicles (EVs). Our expertise in high-tensile materials and lightweighting helps OEMs and Tier 1 and 2 suppliers meet strict durability and regulatory requirements, especially for crashworthiness and emissions reduction goals. ATD’s solutions help customers hit these performance targets without costly rework or failed audits.
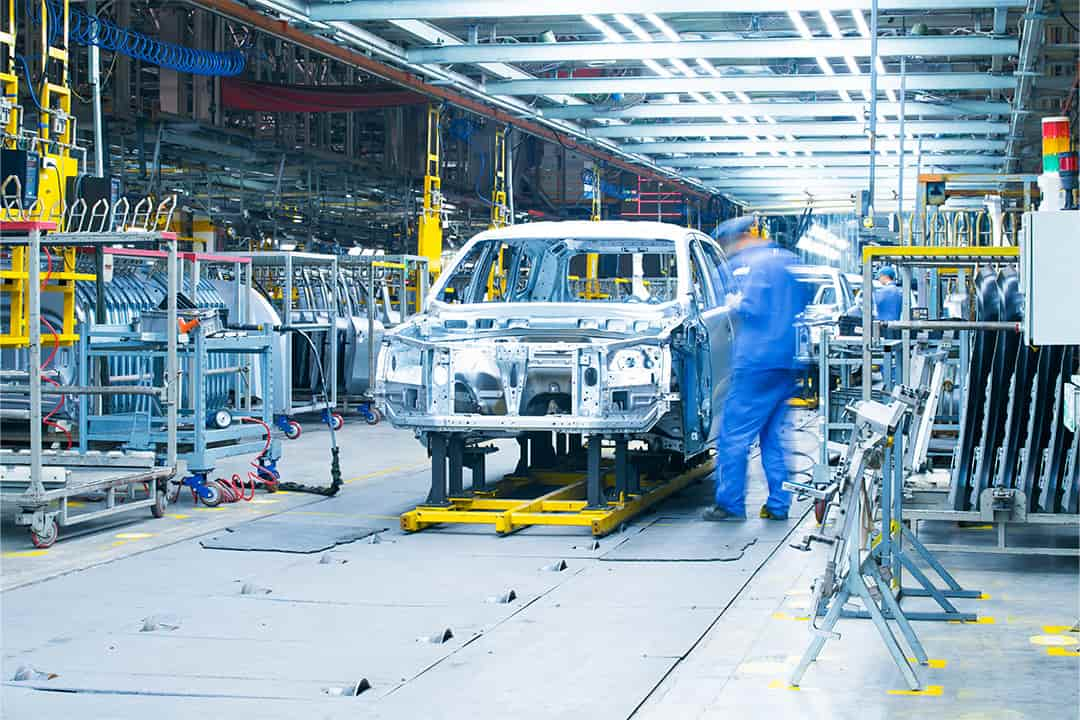
Transportation
The transportation sector demands strength, reliability and corrosion resistance. ATD delivers components for commercial trucks, rail systems and aerospace applications — supporting chassis structures, NVH reduction parts and heavy-duty mounting brackets.
Fleet managers and commercial OEMs need components that can survive decades of vibration, load cycling and weather exposure. ATD's materials expertise and forming capabilities ensure that parts don’t just meet specs on day one — they perform long-term.
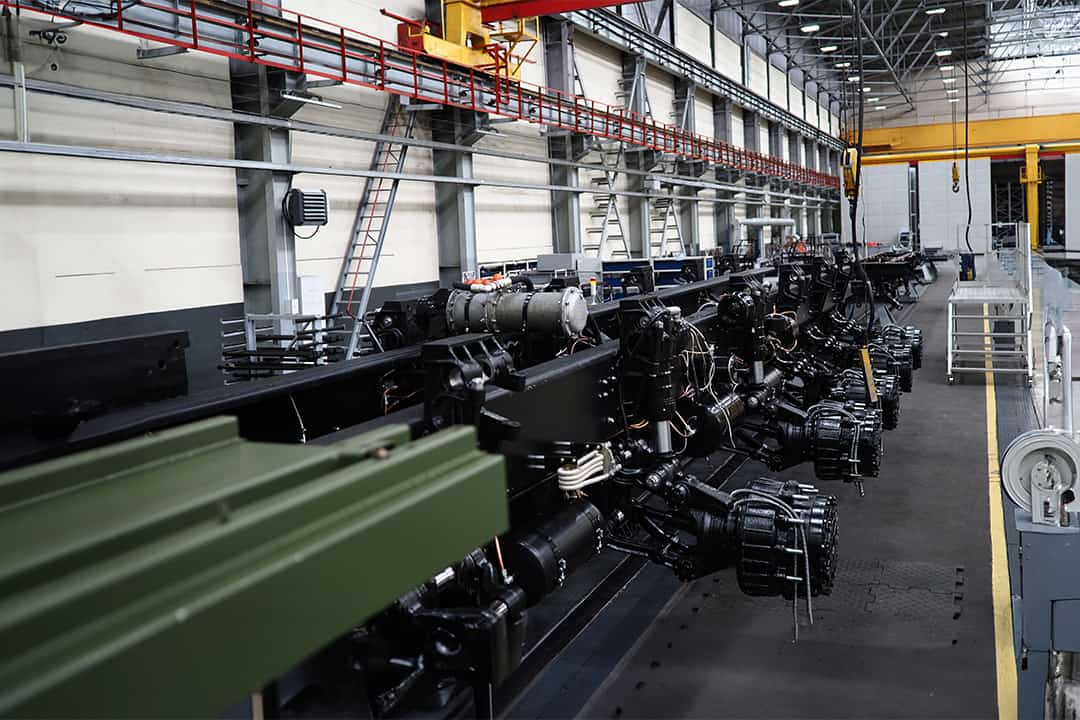
Industrial Hardware & Infrastructure
Non-automotive industries rely on ATD for structural hardware, plumbing components, infrastructure fasteners and more. Our high-tonnage capabilities ensure long-lasting parts that meet the demands of construction, utility and heavy equipment sectors.
Industrial buyers often struggle to find metal stamping partners that understand high-load structural parts. ATD’s engineering-first approach ensures components meet application-specific demands, reducing costly field failures or maintenance callbacks.
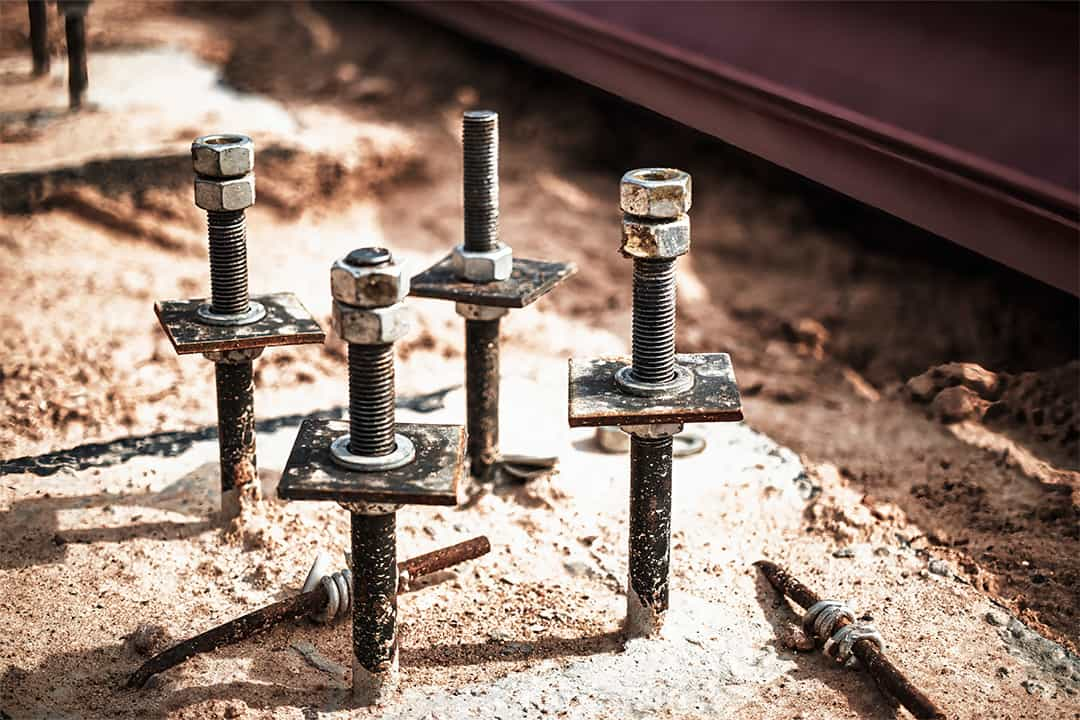
Plumbing & HVAC
Builders, plumbers and OEMs need stamped parts that resist moisture, temperature swings and chemical exposure. ATD’s proven material selection and corrosion resistance strategies help customers deliver long-lasting systems that build brand reputation.
We produce lightweight, corrosion-resistant components such as brackets, pipe fittings and valve housings, essential for plumbing and HVAC applications where durability and consistent quality are critical.
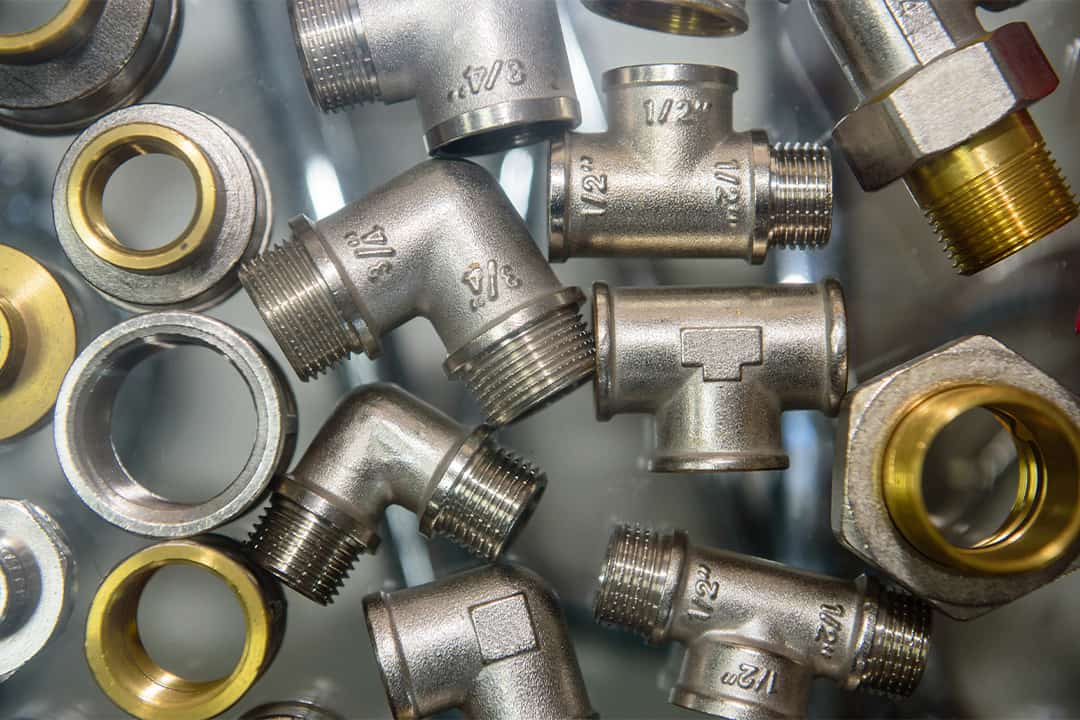
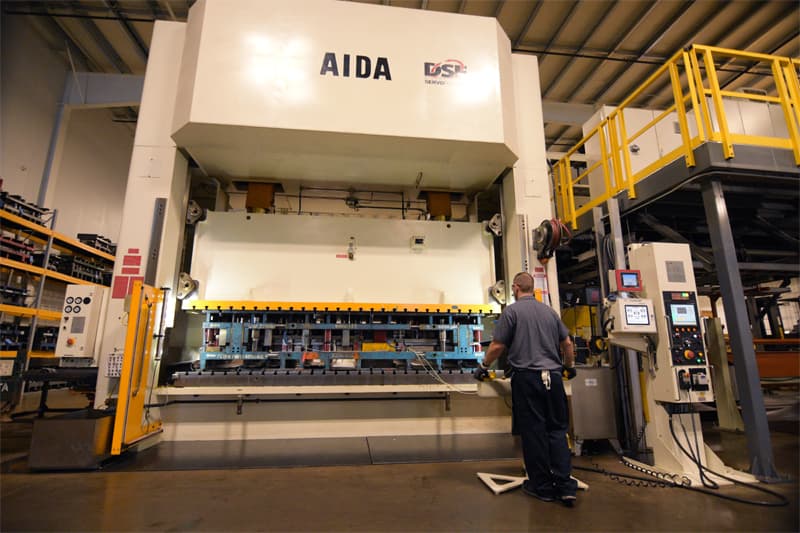
How to Enhance the Quality & Durability of Infrastructure Projects With Precision Metal Stamping
Infrastructure projects depend on durable, corrosion-resistant metal components. Learn how precision manufacturing strengthens construction.
.jpg)
5 Heavy-Duty Construction Stamping Solutions You Need to Know About
Heavy-duty construction projects require stamped components that can stand up to extreme loads and tough environments. Learn about five critical metal stamping solutions ATD provides for long-term performance in construction applications.
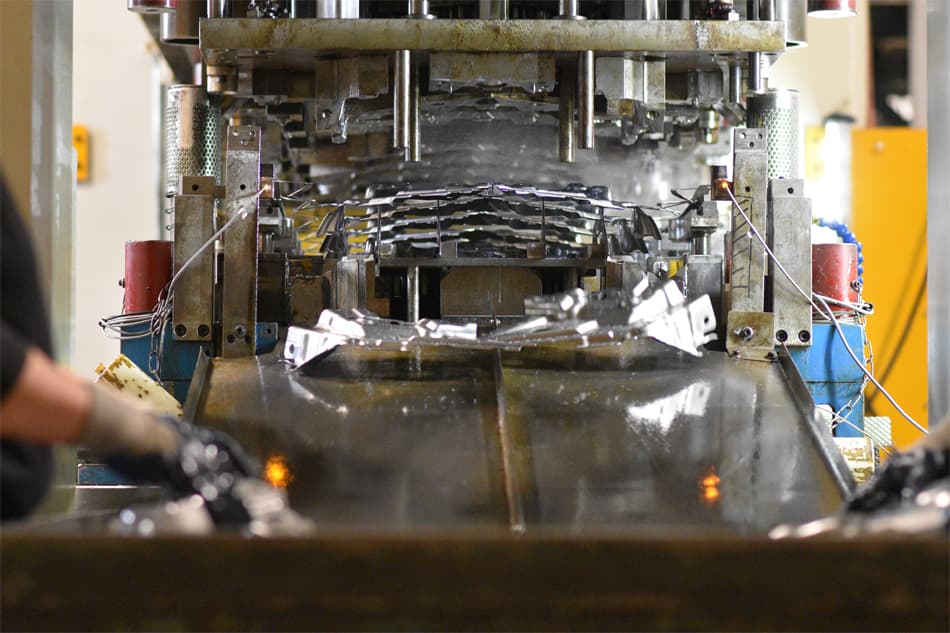
Why High-Tonnage Presses Are Essential in Electric Vehicle Component Manufacturing
Electric vehicle production demands lightweight, durable parts manufactured with precision and speed. Learn how ATD’s high-tonnage stamping presses support the growing needs of EV manufacturers around the world.
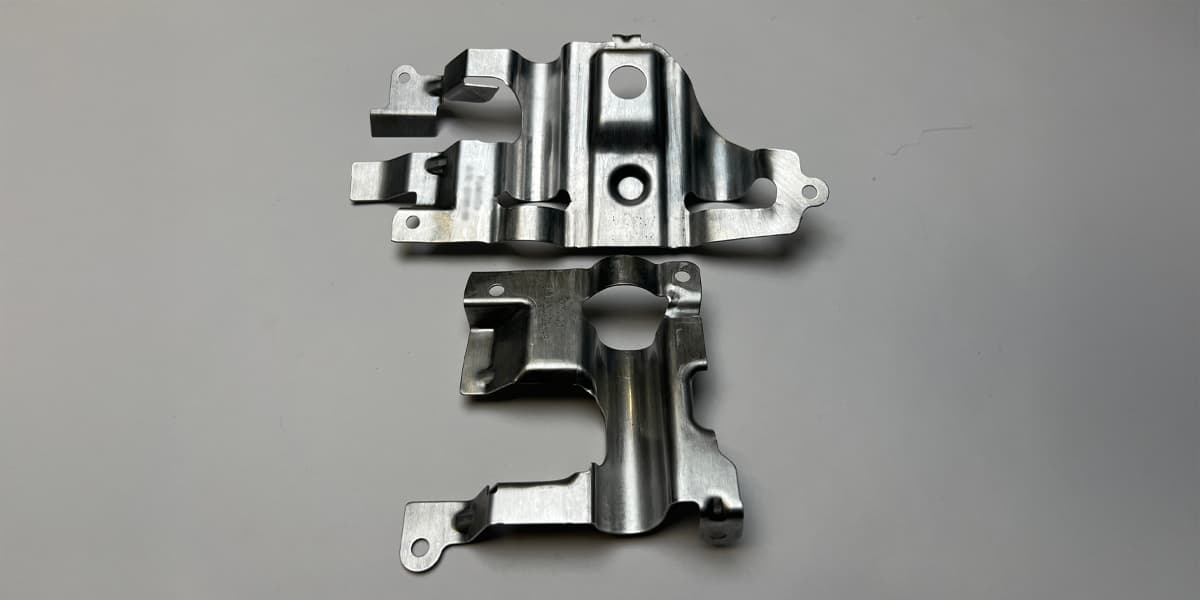
Why Aluminum Stamping Is the Key to Unlocking Strength & Efficiency in Lightweight Automotive Structures
Lightweighting is critical in automotive design — but strength and safety can’t be sacrificed. Explore how ATD’s aluminum stamping solutions deliver strong, lightweight parts that meet modern automotive performance standards.
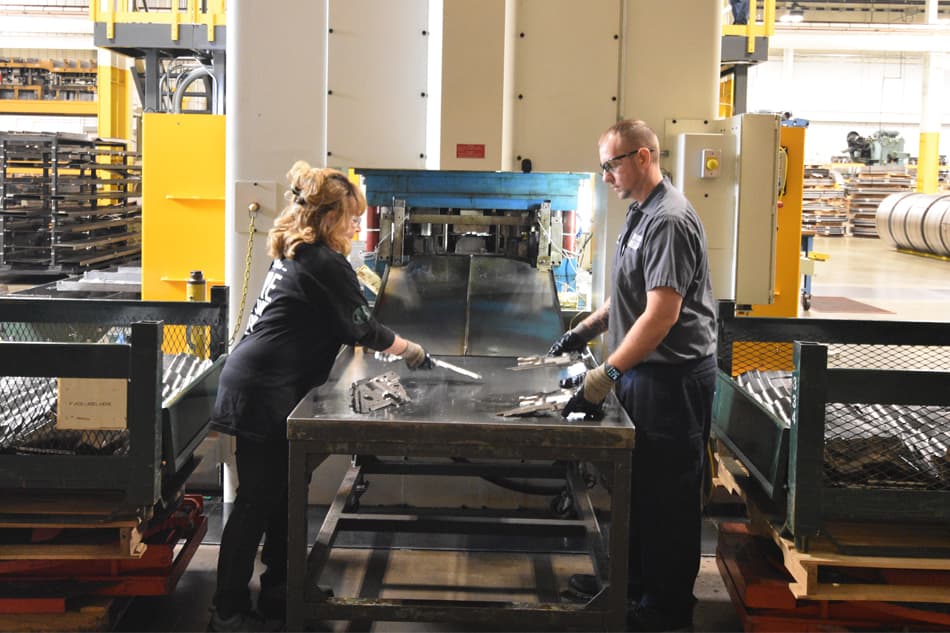
How High-Precision Metal Stamping Presses Maximize Efficiency in Automotive Parts Manufacturing
High-precision metal stamping presses support faster production speeds, consistent part quality and lower material waste. Find out how ATD’s technology helps automotive manufacturers improve manufacturing efficiency without sacrificing quality.
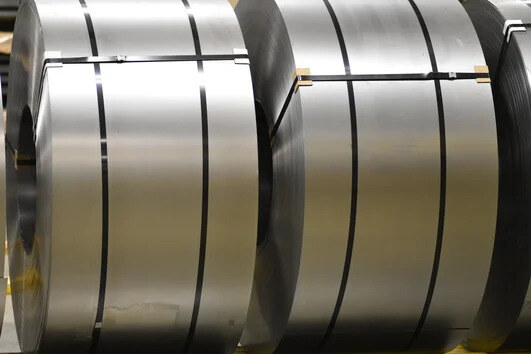
Galvanized Steel Stamping — Combining Corrosion Resistance & Strength for Automotive Excellence
Galvanized steel is essential for automotive components that demand both durability and corrosion protection. See how ATD’s precision metal stamping processes deliver strong, reliable parts for today’s toughest automotive environments.
Quality Control in Manufacturing
Skilled Technicians in Metal Stamping
Quality control in manufacturing is only as strong as the people behind it. ATD’s skilled technicians are experts in die setup, in-process inspection and final part verification. Certified to IATF standards, our manufacturing teams use process-driven techniques to maintain consistent part quality across all production runs.
Many manufacturers lose time and money on rework and scrap due to inconsistent production standards. ATD’s deeply experienced technician team prevents these issues before they can start — saving customers significant operational costs over the long term.
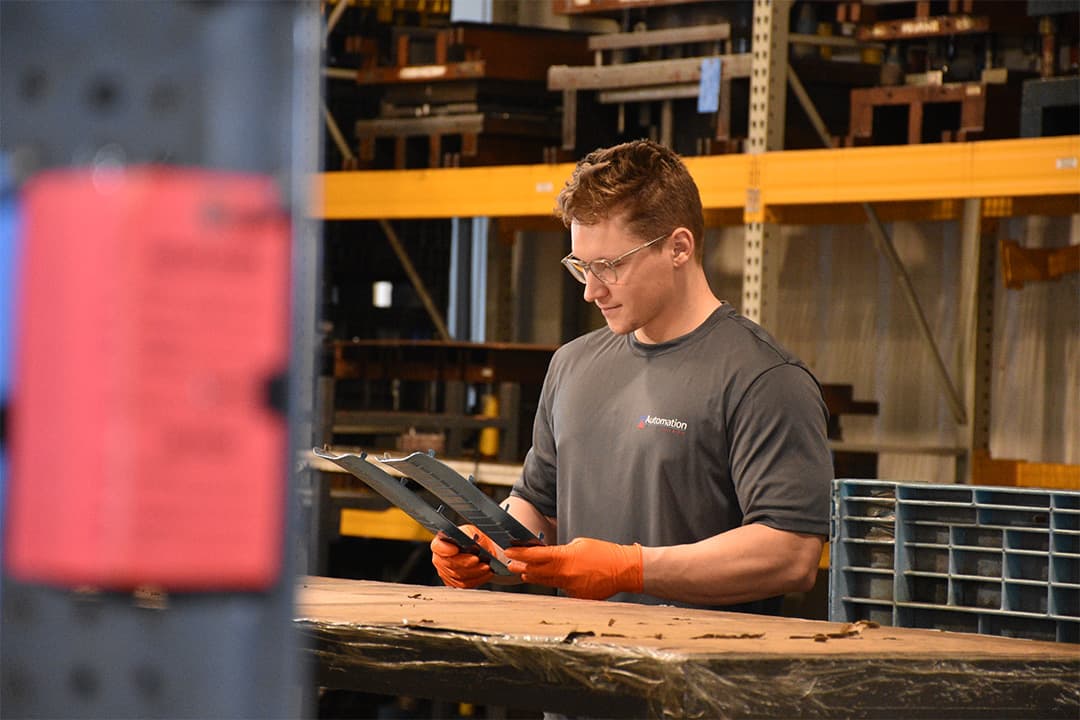
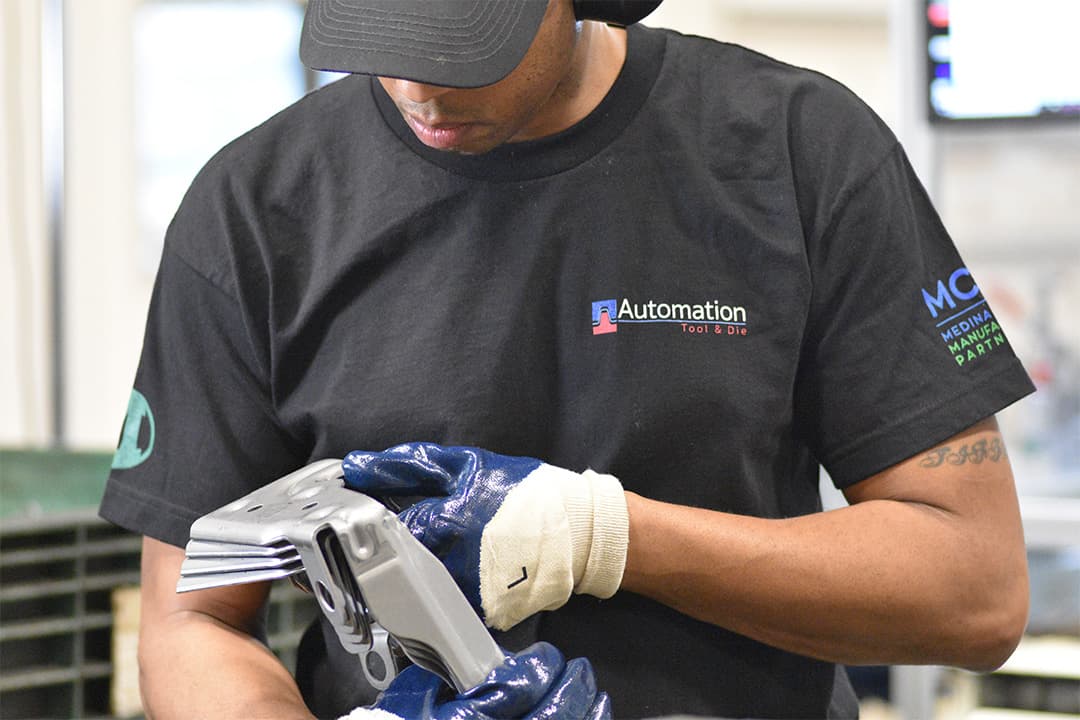
Die Setup Best Practices for Reliable Production
Accurate die setup is the foundation for consistent part quality. ATD’s skilled technicians follow proven best practices during die installation and setup, including:
-
Careful die alignment for uniform force distribution
-
Rigorous die inspection before and during installation
-
Validation tests using sample parts to confirm correct stroke pressure, shut height and feed alignment
This upfront attention prevents common production issues, such as uneven metal flow, incomplete cuts or tolerance drift, which could impact part quality and consistency. Mistakes in die setup not only affect the current run, they can damage tooling and cause expensive downtime. ATD's preventive attention ensures that critical, often overlooked setup steps are never skipped, delivering more uptime and greater throughput for customers.
In-Process Inspections That Catch Issues Early
ATD integrates frequent in-process inspections using both manual gauges and automated measuring equipment. During production, technicians:
-
Measure key dimensions on a statistically significant sample of parts
-
Monitor material flow, thickness and forming during progressive stamping
-
Review press force signatures for any anomalies
Catching minor variations early prevents scrap accumulation and costly rework, maintaining manufacturing efficiency and quality from the first part to the last. By using Statistical Process Control (SPC) techniques, ATD can track and react to even the slightest drift in production variables, well before they would cause rejects. Customers benefit from steady, predictable part output, even in very large production volumes.
Final Verification Through Advanced Metrology Tools
Before any lot is approved for shipment, ATD performs final inspections using high-accuracy metrology tools. This includes:
-
CMM (Coordinate Measuring Machine) dimensional checks
-
Surface finish assessments
-
Hardness and material verification if required
Final verification guarantees that every part shipped meets or exceeds customer specifications and industry standards. Shipping nonconforming parts can result in massive liability and supply chain disruption for customers. ATD’s final verification acts as a last line of defense, protecting customer production schedules and preventing expensive field failures.
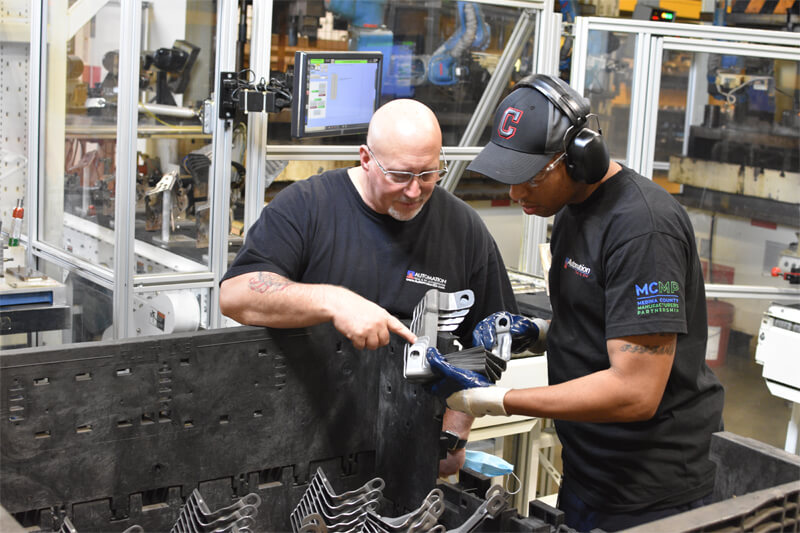
How Skilled Technicians Can Elevate Tool & Die Manufacturing
Skilled technicians are essential to delivering consistent quality control in manufacturing. Learn how ATD’s teams keep parts accurate and reliable.
Prototyping Solutions
Prototype metal stamping is critical for reducing development risks and verifying designs before full-scale production. ATD’s facility is built to support fast, high-accuracy prototyping solutions that prepare customers for a smooth transition to volume manufacturing.
In today's fast-paced markets, time-to-market can determine success or failure. ATD’s prototyping services are structured to accelerate customer timelines without introducing quality risks — allowing manufacturers to move faster, smarter and with greater confidence.
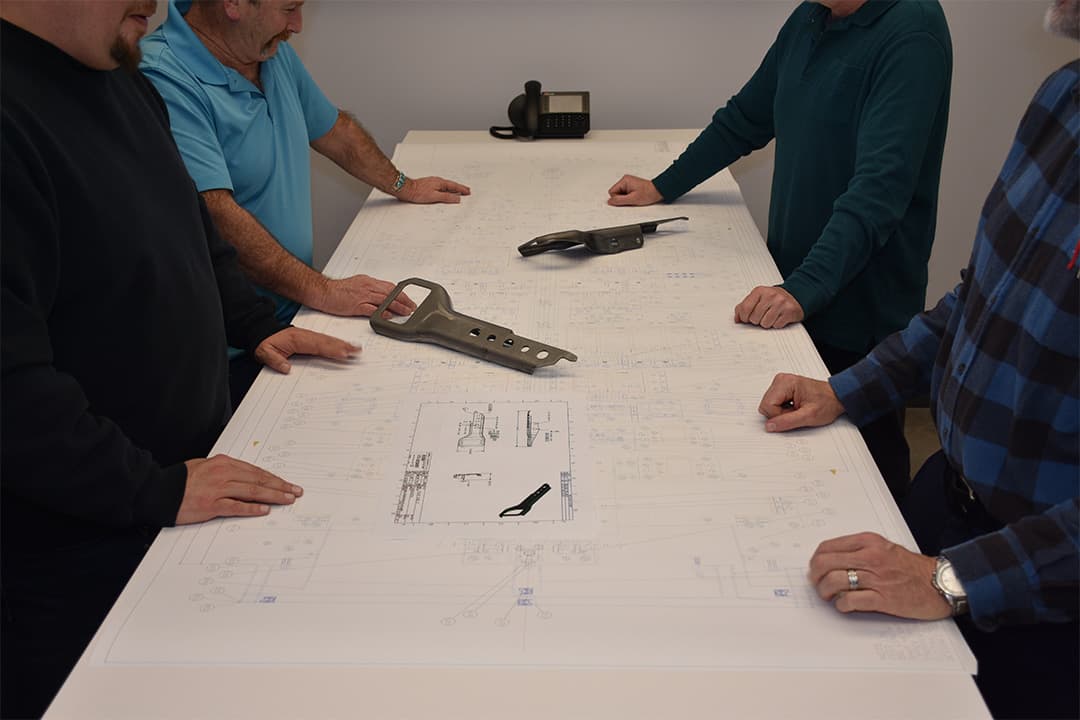
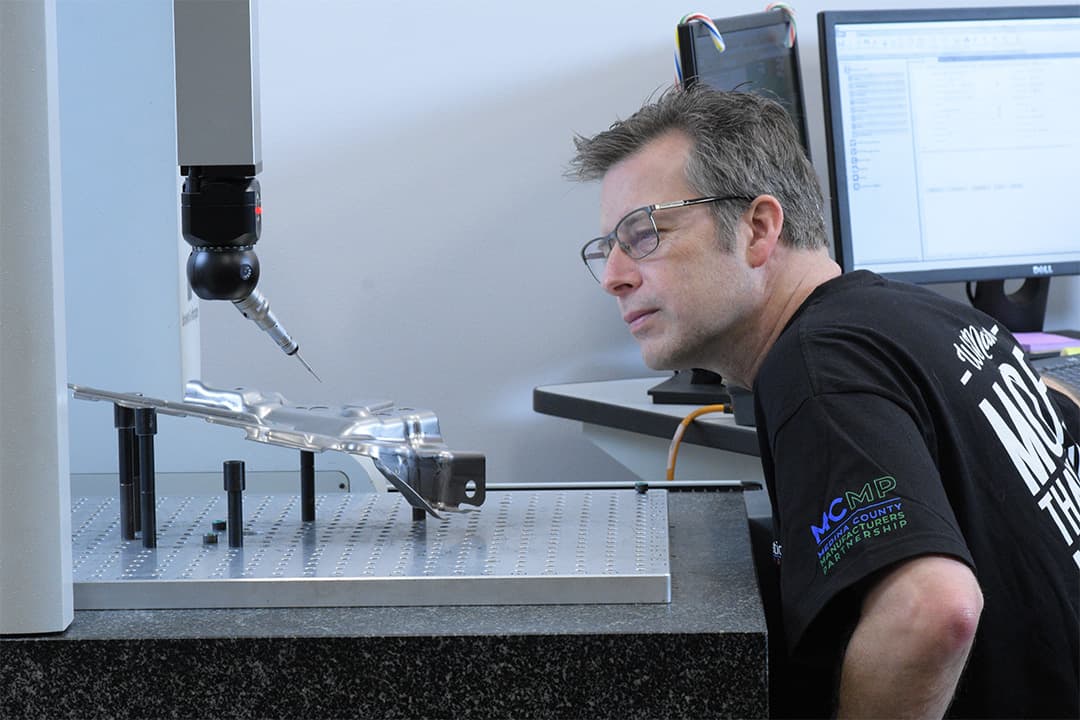
Facility Efficiency for Prototype Metal Stamping
Rapid Prototype Part Production
Speed is critical in early-stage product development. ATD’s prototype metal stamping team works quickly to deliver first article samples without sacrificing part accuracy. Our facility allows for:
-
Fast die modifications for prototyping needs
-
Small-run production using both mechanical and servo presses
-
Quick changeovers between prototype and production tooling
Rapid prototyping reduces development cycles and provides critical real-world validation early in the process. Customers often cite long prototype timelines as a barrier to innovation. ATD’s flexible press scheduling and modular tooling approaches cut days or weeks off the prototype cycle, keeping new product introductions on track.
Accurate Representation of Final Part Specifications
Prototype parts from ATD are engineered to mirror production-quality parts as closely as possible. This is achieved by:
-
Using production-grade materials whenever possible
-
Stamping with the same tonnage and press settings planned for production
-
Building prototype tooling that mirrors production dies
Manufacturers who receive prototypes that don't behave like production parts risk expensive design changes late in the process. ATD’s consistent prototype-to-production method prevents this risk, giving engineering teams confidence early on.
Early Collaboration to Support Manufacturability & Durability
ATD’s team collaborates closely with customer engineering teams from the start, offering manufacturing feasibility input that avoids costly late-stage revisions. Early collaboration helps:
-
Refine part designs for stampability
-
Minimize costly secondary operations
-
Validate material choices for durability, strength and corrosion resistance
Many design teams underestimate the complexity of manufacturing certain geometries. By involving ATD early, customers avoid late-stage surprises that could delay launches or spike production costs.
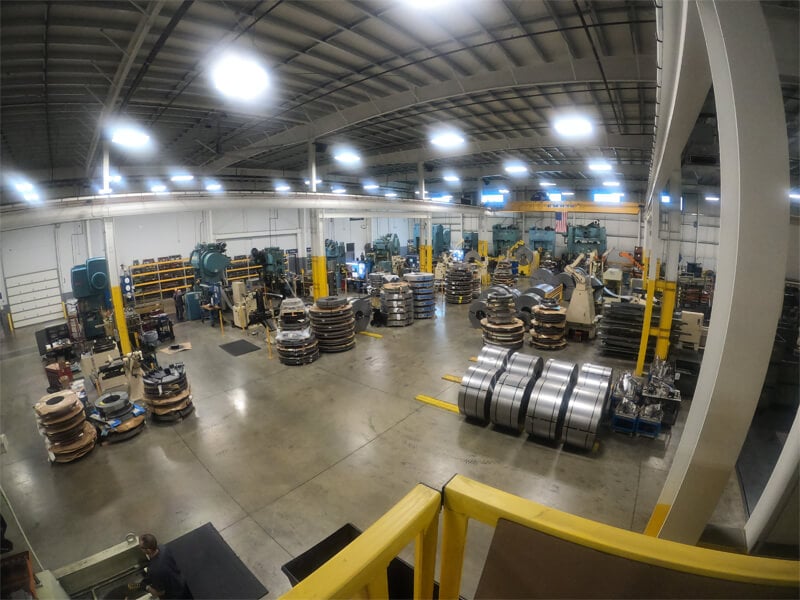
How Automation Tool & Die’s Facility Is Optimized for Peak Efficiency
Facility layout matters for prototyping solutions and full-scale production. See how ATD’s workflows drive manufacturing efficiency.
Manufacturing Efficiency in Production
Manufacturing efficiency means faster output, lower costs and consistent quality — all without sacrificing part performance. ATD supports high-volume manufacturing with advanced presses, tooling systems and a strong focus on repeatable quality.
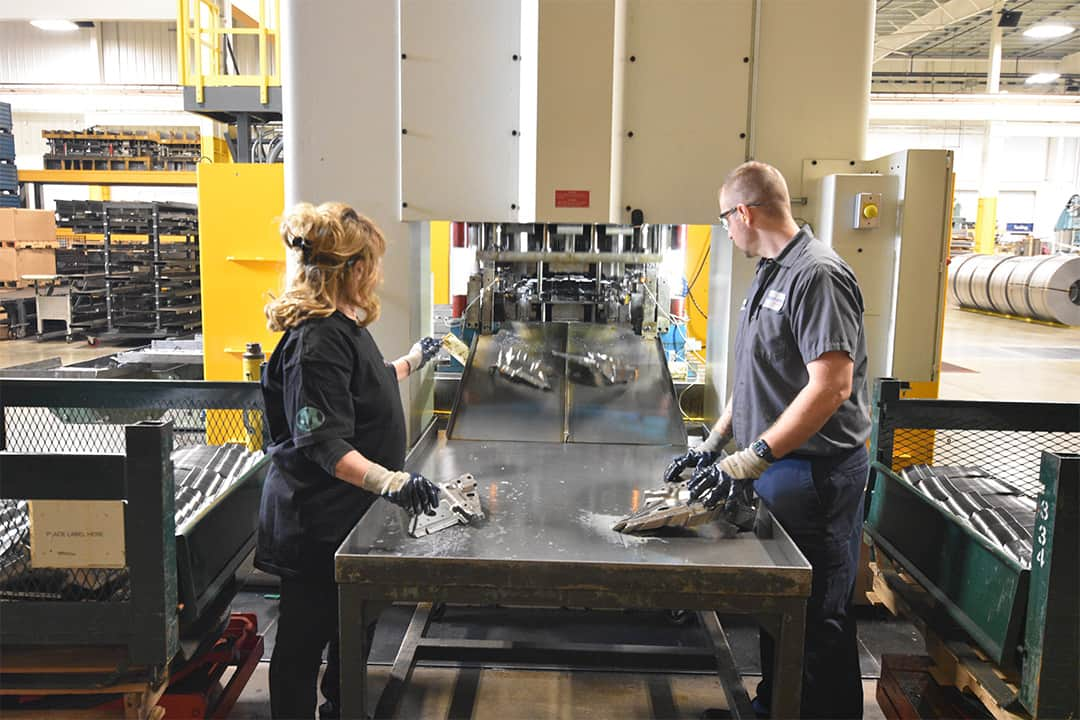
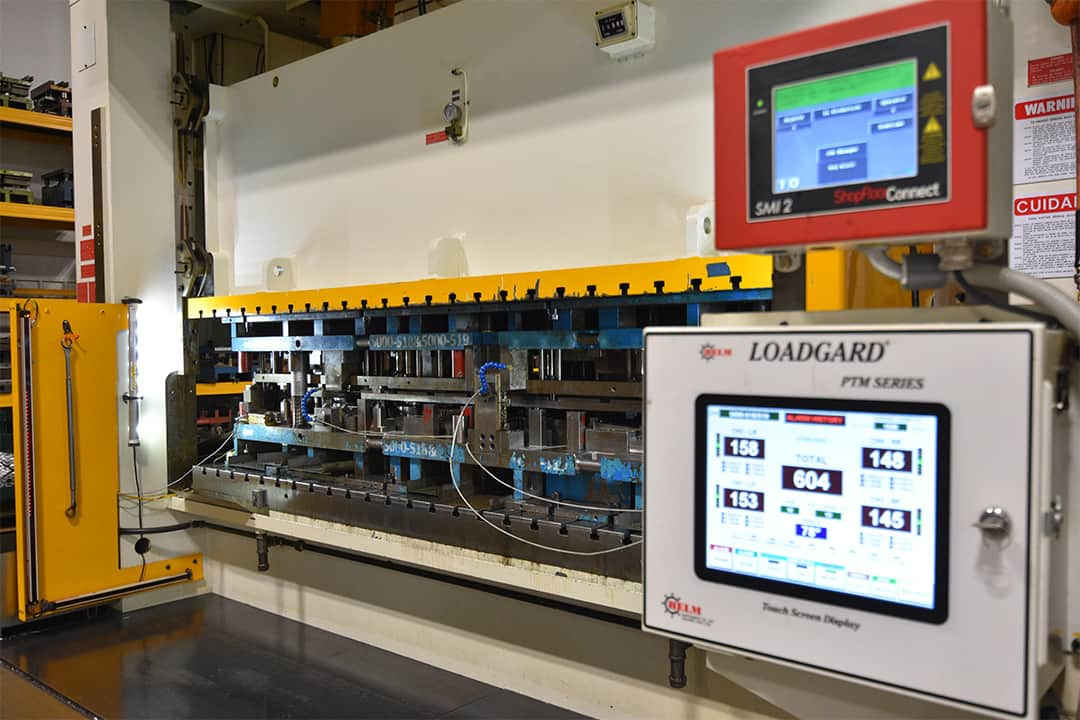
Servo Press Technology
Servo presses allow greater control over stroke speed, pressure and forming sequences compared to traditional mechanical presses. At ATD, servo presses are used to:
-
Achieve complex forming requirements
-
Improve metal flow for lightweight and high-strength materials
-
Reduce part variability during multi-stage stamping
For customers focused on lightweighting, achieving complex forms without cracking or thinning is critical. ATD’s servo press expertise ensures lightweight parts are stamped reliably, reducing material costs while meeting safety standards.
High-Tonnage Presses and Scalable Production Systems
Manufacturing efficiency is critical in meeting growing demands across industries such as automotive and industrial equipment. ATD’s high-tonnage presses, ranging up to 700 tons, allow us to manufacture large, complex components efficiently, while our servo presses support detailed, precision-critical parts at high speeds.
We achieve manufacturing efficiency by:
-
Streamlining die setups for faster production transitions
-
Using servo press control systems to maintain part consistency
-
Minimizing scrap and downtime through in-process verification
ATD's production system is designed for continuous output without sacrificing the precision required for high-performance applications.
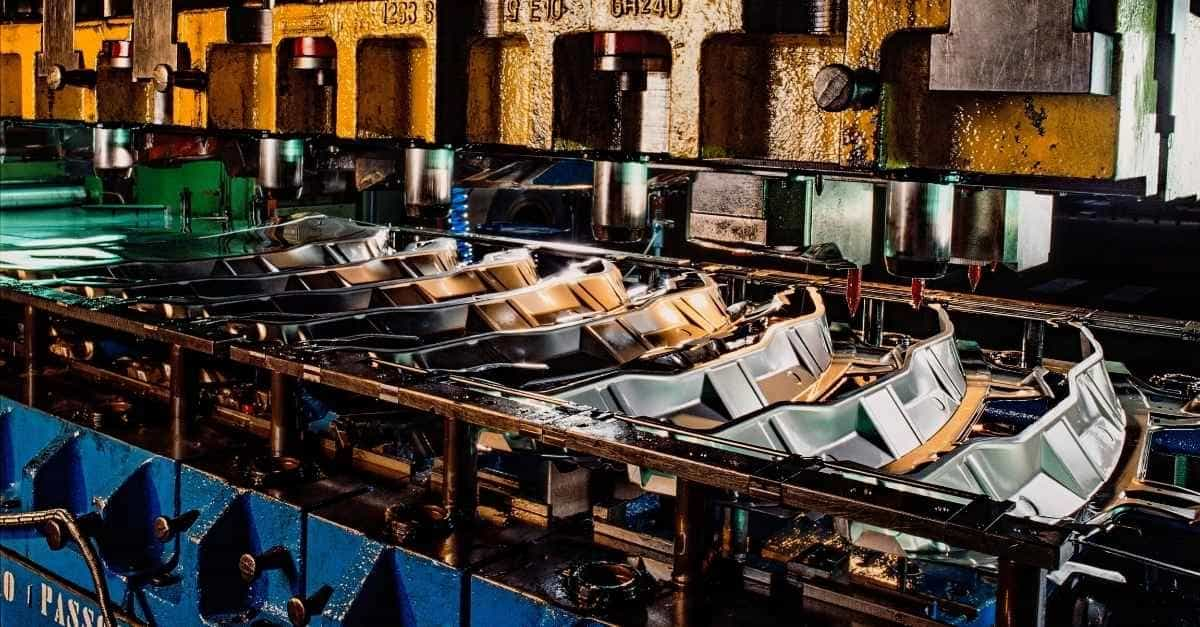
How Advanced Servo Press Technology Enhances the Forming & Bending of Complex Geometries
Complex geometries require the right technology. Learn how servo presses deliver precise forming for safety-critical components.
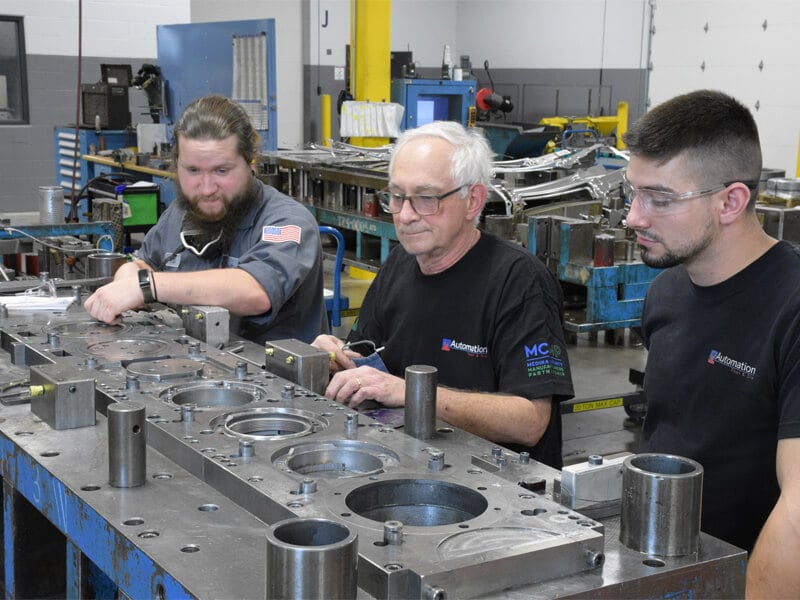
How Manufacturers Should Approach Collaboration
Collaboration between manufacturer and customer supports higher quality, faster delivery and better production outcomes.
Meeting Demand Without Compromising Precision
ATD’s production strategies are designed around:
-
Reducing downtime between production runs
-
Achieving high repeatability and consistent quality
-
Supporting lightweighting trends and EV production with precision metal stamping
Our collaborative process ensures customers have a clear line of communication throughout manufacturing, minimizing risks and supporting smoother production schedules.
Work With ATD for Precision Manufacturing Solutions
Whether producing high-strength EV components, corrosion-resistant industrial hardware or safety-critical automotive parts, ATD’s precision manufacturing capabilities help customers achieve consistent results. Our focus on quality control in manufacturing, effective prototyping solutions and scalable production systems makes us a trusted partner across industries.
By choosing ATD, manufacturers gain a strategic partner focused on consistency, efficiency and long-term success. Looking for dependable precision metal stamping and manufacturing support? Request a quote.
Discover What We're Capable Of
Partnering with ATD means receiving the quality products, services, timeliness and problem-solving support you need to win more customers.